Rob & Carol's Eagle
new canvas
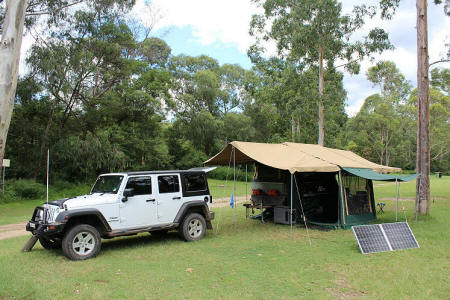
self sufficient camping
We
picked up our 1990 built pre-loved Track Trailer Eagle two weeks before Easter
1993. The camper was owned by the Track Trailer agent here in Newcastle. Back in
those times it wasn't uncommon for someone to make their camper available for
inspection to a prospective buyer as an agent of the manufacturer. They were
selling their Eagle & moving to a rear flipover hardfloor which had easier
access to the bed.
After all these years we are still very happy with our Track Trailer Eagle
& seeing there was nothing that really
caught our eye for an upgrade, we thought last year we would give it a birthday
& put new canvas on. What
really makes the camper for us is the dust proofed locker system making for easy
storage, plus the 6ft x 4ft trailer storage area.
There were
plenty of changes & ideas we had thought of over the years that would make for a
more comfortable camper trailer. All Terrain Camper Trailer's 14foot model was
very close to what we had in mind & with a few tweaks we would have a camper
that suited us down to the ground. We had a chat with Glen & Trish about our
needs & a plan was devised.
The internal floor space
is around a metre wider than the original Eagle tent, giving us more space for a table &
two chairs when having a meal out of the weather with the lockers open to the
internal kitchen. The zip out floor is made
from heavy duty vinyl & is a great idea for removing to hose over after camping in
wet & muddy conditions.
The new camper tent is made
from Australian made 14oz Wax Converters canvas & has plenty of ventilation via the
large midgee mesh windows in each wall. The large windows also allows plenty of
light inside giving it an open airy feel. All window awnings are zipped from the outside
& with velcro tabs across the bottom. The moon roof allows any heat to
escape on a hot day while drawing cooler air from under the trailer itself via
vents in the PVC drop off the camper. There is a clear PVC cover on the
main side window that can be rolled down to provide light inside the tent area on rainy days.
We wanted large screened doorways each end that open onto the
awnings front & rear, plus a third awning that can be zipped on either end.
Coupled with these & with four
walls, provide plenty of shelter from the sun on a hot day or a large dry area
when the rain sets in. We leave the rear awning on all the time & lift it onto
the main roof with a tent pole, then dragging it over the top with two permanently
attached ropes on the corners. If staying overnight we can pull the awning out
in quick time when needed depending on the weather. We only zip the front awning on
if staying for a few days. The two awnings have proved useful if the weather
blows up.
The dust proofed locker
system is built using monocoque construction techniques & sits on top of the trailer. The two
lockers on the
drivers side make an ideal food pantry, while the two passenger side lockers,
which are inside when the tent is erected, are the hub of the kitchen with
stove, crockery & cutlery. The kitchen is easy accessible for a quick
roadside stop by lifting up the travel cover. The front locker holds our spares, tools
& 12volt leads etc.
I have added extra shelving to all the lockers providing better packing & also making it easier to find the item you are looking
for.
The
foam bed sits on top of the camper between the lockers ready made. We prefer
fitted sheets & have a woolen underlay with a down duner over the top for winter
warmth.
I built two large ply boxes that slide into the
rear of the six foot long box trailer. This provides a huge additional storage space for our
clothes, cooking, camping gear etc.
The
maintenance free, hot dipped galvanised, off road Guiding Star trailer itself is
virtually bulletproof & has not let us down despite the punishment it has
received over the years. The chassis is
fabricated from RHS with a 3mm wall thickness while the 60
series Landcruiser leaf suspension comprises of seven leaf springs by 70mm
wide with an eye to eye measurement of 1040mm. Those travelling behind us are
amazed at how well the trailer behaves. The Koni
shocks were a little long in the tooth with one leaking, so I replaced them with
Tough Dog shocks, the stroke & compression of which matched the front end of a
Landrover. The suspension combination works extremely well in all road
conditions. Off road the trailer is well behaved & negotiates tight situations
easily owing mainly to the short draw bar & rear set axle.
While
we did not have a complaint with the nine inch hydraulic overrider brakes, we
did have to replace them as we could not open the rear door of our new Jeep JK
Wrangler when hooked up because of the hydraulic master cylinder's position on the trailer.
I installed a 10 inch electric braked Vehicle Components 45mm square axle that
is rated at 2 tonne because of the parallel bearings used. The
original 45mm square axle used Holden tapered bearings & was rated at 1.3 tonne.
I
also installed a Redarc EBRH brake controller with remote head. With limited
room in the JK Wrangler the EBRH was the perfect choice. The main body is mounted
in the dash cavity while a dial & small light is the only visible controls
you have on the dash itself.
Even
after raising the rear door mounted spare on the JK Wrangler we still had to
push down the Tbar on the reliable 20 year old Treg coupling to clear it. There
was only
one solution & that was a new low profile coupling. I installed a Vehicle Components DO35 V2
coupling which has proved a pleasure to use. The second version
incorporates a dust cap. I also installed a Vehicle Components side mount
handbrake.
A
removable rack sits across the front of the trailer that carries three 20 litre jerry's of either water or
fuel
depending on the trip. The 60 litre
water tank is situated under the rear of the trailer, encased in a steel
protective cover, supplying water through two hand pumps, one in the kitchen
locker & the other located on the rear outside drivers side guard.
There
is a battery box on each side of the trailer & I managed to squeeze in a 120 amp
hour AGM battery into each. The passenger side box has access when the camper in
erected through a zipped door in the PVC side drop. There is a six fuse outlet
which has both a positive & negative bus bar for easy connection to outlets.
Seeing
most 12volt accessories come with a cigarette lighter plug, we have found them
ok for the low drawing accessories we use around camp. Each 12volt socket has a
short run in 5mm
auto cable & has its own fuse.
The
drivers side locker has the Redarc BCDC1225 DC-DC charger along with a voltmeter. The
BCDC1225 charges the camper trailer batteries from the vehicle's alternator
while driving using multi stage charging technology & when camped using the MPPT
side of the charger via our portable 130watt Kyocera panel. A 240volt 25amp
charger maintains the batteries at home.
Dust
entry under the travel cover had always been a problem mostly due to the way the bungie cord was used
to secure it. I came up with the idea that if a PVC skirt was
placed across the back under the travel cover slotted into a length of sail
track, this would prevent the canvas being covered in dust. After many kilometres of dirt road this has proved
successful.
The
front also had a similar problem. I had a length of PVC sown above the bungie
cord. The skirt then wraps under the leading edge of the camper & is once again
held in place with bungie cord. Simple & effective.
Rob & Carol
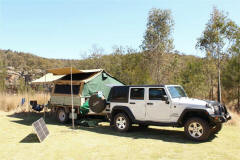 |
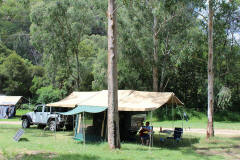 |
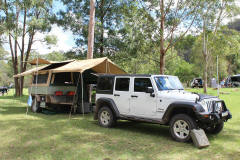 |
one awning
stopover |
plenty of
undercover area |
undercover
access |
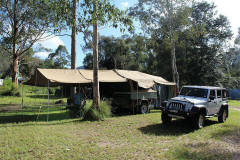 |
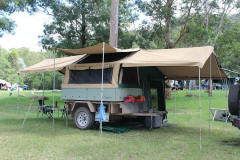 |
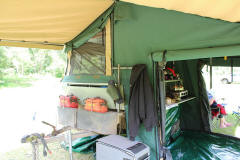 |
double awning |
hot air escapes
via moon roof |
front awning
area |
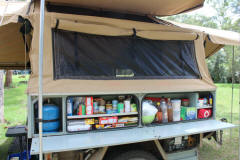 |
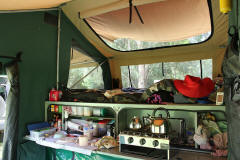 |
 |
drivers side
lockers |
kitchen |
drawing cool air |
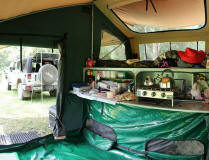 |
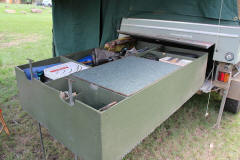 |
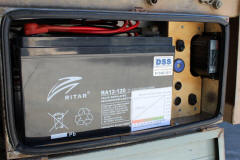 |
open & airy |
trailer storage
boxes |
drivers side
battery box |
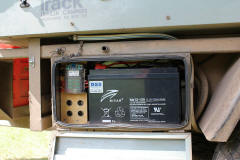 |
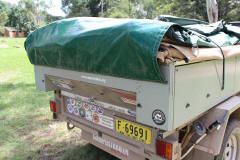 |
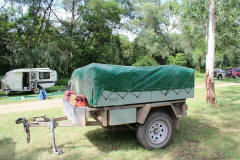 |
passenger side
battery box |
rear dust cover |
ready to hookup |
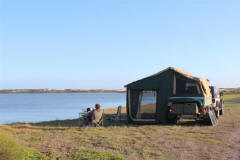 |
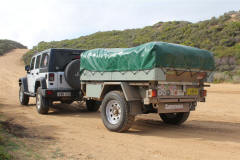 |
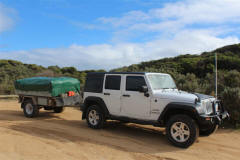 |
quick overnight
stop |
easy to tow |
& compact |
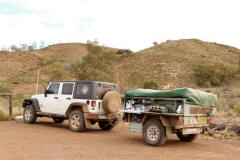 |
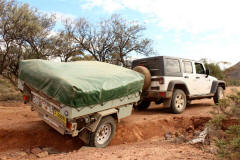 |
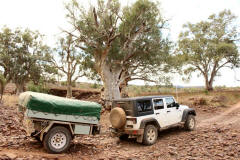 |
lunch stop
|
off road ability |
soaking up the
bumps |
march 2013
|